
- #Dynamic response of stack piezo actuators generator#
- #Dynamic response of stack piezo actuators code#
The main clock has a frequency of 100 MHz, generated by an internal PLL fed by an external 50 MHz oscillator.Īll the state machines and processes are synchronized by the main clock, and some internally generated clock enable signals are used to schedule the algorithms.
#Dynamic response of stack piezo actuators code#
The entire FPGA project takes up to 12 k logic elements (on a maximum of about 33 k available on the ALTERA Cyclone II device used in the application) divided into 18 main entities the implemented code uses about 150 kbits of the memory embedded on the FPGA and 4 DSP elements for the fast fixed point multiplications. The power board is also provided with a boost DC/DC converter also controlled from the same FPGA device in order to make the system compliant with automotive applications where the standard 12 V power source is not useful to drive the piezoelectric actuators.
#Dynamic response of stack piezo actuators generator#
A good method to drive a capacitive load is to use a current generator driven by an external signal: the simplest way to implement this type of current generator is to use a transconductance amplifier driven by a PWM signal (see Figure 6). Hence from the charge stored in the piezo equivalent capacitance, it is possible to estimate the needle position.įrom the models above, it is possible to consider the piezo stack as a capacitive load. (2)an outer loop which controls the charge stored in the injector. (1)an inner loop which controls the injector current, The implemented control is based on two different feedback loops: Nevertheless, loaded charge is proportional to the current transferred to the piezo stack by the power driver. A direct charge measurement is also possible but it is an intrusive technique. The constitutive equations of a piezoelectric stack showed that the needle position is strictly related to the electrical charge loaded in the equivalent capacitance of the injector itself.
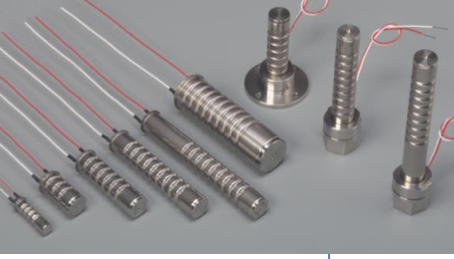
So, in order to estimate the injector needle position, it is important to measure a related quantity. Unfortunately, no velocity, position, or force measure can be performed inside the injector, neither on the piezoelectric stack nor on the leverage. This can be done by performing a position control on the injector needle. Injector controller is aimed at the control of the fuel quantity injected in the combustion chamber of the cylinders. Reducing the mechanical model, it is possible to convert it into a frequency domain as shown in (5) as equivalent admittance. The goal is to obtain electrical impedance in order to know the load to be applied to the power driver. Considering only the resonances in the frequency range between 10 Hz and 100 kHz, the model has been reduced to the first five modes. It is possible to transform the nodal equations into modal equations in order to consider each mode independent from the others. (viii) is the equivalent piezo capacitance, (vii) is the voltage drops on piezo stack, (iv) is the electromechanical coupling matrix, (iii) is the stiffness matrix (open circuit ), (ii) is the stiffness matrix (short circuit ), The meaning of each symbol conventionally used in previous expressions is the following: Mechanical and electrical dissipations are not considered during this step. If we consider charge driving, the equations of the stack are Once defined the potential and kinetic energy associated to the element, it is possible to obtain the two electromechanical equations that regulate the behavior of the piezoelectric element.
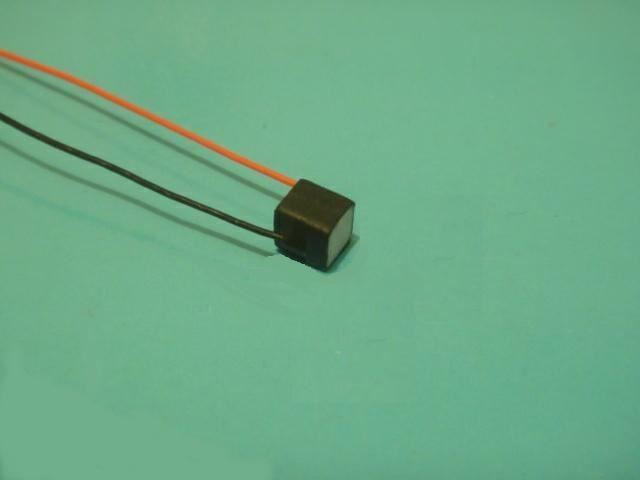
Applying a voltage to the electrical leads of the stack will cause a displacement of the mechanical sides and a force on the faces that are respectively the sum of displacements and forces of each layer. Electrically speaking, the layers are in parallel, while from a mechanical point of view they are in series. The core of the actuator is a stack of piezoelectric layers. The relations that regulate the behavior of the entire piezoelectric actuator are derived from a classic FEM approach based on the standard defined equations.
